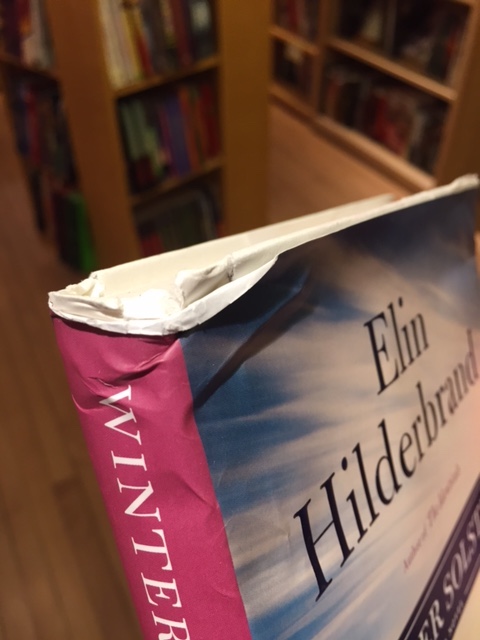
This was a recent doozy. The customer service folks at the distributor we received this from were SO helpful about the damages in this shipment, and genuinely wanted to figure out how they had happened.
October is the biggest month of the year for new releases, which I suspect accounts for the wild uptick in damages we’ve seen in shipments lately. More books = more hands needed in warehouses, which means more temporary or new employees with less training and experience in packing books so they don’t smash each other on the way to bookstores. I have to say, I really feel for packers in warehouses, because they’re spending all day packing zillions of books into boxes at great speed. I don’t think anyone is intentionally careless or sloppy, but I do think that better practices and less time pressure might have better results—which could save big money in the long run.
It seems to me that one of the most cost-effective measures cash-strapped publishers could take is a really simple one: make sure your warehouse staffers are well trained and use effective packing materials and boxes that truly protect your books. I’m sure untold thousands of dollars and hours have been spent researching the best practices for book shipments, so I’m always surprised when we come across poorly packed boxes with expensive books loosely sliding around. A few pieces of fill paper won’t do much to protect that art book with the ivory textured matte cover (note to art departments: please don’t design light-colored matte dust jackets unless you plan to shrink-wrap books or don’t mind absorbing a lot of damages; these get so dirty sitting in warehouses, and not all of the grime erases off).
One of our first employees, Roman, used to work in receiving at a big bookstore, and he taught us that placing books spine against spine in boxes helped keep those open sides from jamming together. So simple, but for some reason, most people pack books with the spines up against the box edges, open pages facing inward. Once you think about it, it makes so much more sense the other way.
Damages are really expensive for publishers, who have to either replace them or give credit to bookstores, and often, publishers send “call tags” (prepaid mailing labels) to pick up damaged books from bookstores, which costs them money as well as customer service and warehouse time.
Damages are costly to booksellers, too. Not only do our staff spend a lot of time calling or emailing publishers to report damages and packing up injured books to return, but we have to assess each book to determine whether or not the damage is bad enough to affect its salability, and guess whether the customer who ordered a book that arrived damaged will still want it (at a discount, the cost of which we, the bookstore, absorb). Frustratingly, it is often the expensive special orders that arrive with damages. It always seems to be the $50 book we’ve ordered one copy of that has the ripped cover or crushed corner, and the book that a customer MUST HAVE as soon as possible.
We have two main criteria for assessing whether a book is damaged enough to warrant being returned:
- Is the bend / tear / goo / smudge / dent / ding / wrinkle / crush noticeable enough that a customer wouldn’t choose it as a gift? (We are a little more forgiving of slight damages to books people buy for themselves, but when people pay for brand-new books, they do tend to expect them to look brand new.)
- If we don’t report that damage and the book doesn’t sell, and we then try to return it to the publisher, will the publisher reject it for being damaged? If that’s a possibility, it’s not worth risking.
When books arrive damaged, both publishers and booksellers face disappointed customers and spend valuable staff time and money processing the returns and paying for the damages. If there’s any room for improvement at your warehouse, that’s not a place to cut corners. A little extra time and training could make all of our holidays brighter.
And publishers, we do appreciate the challenge. And it’s not always the fault of the packing; sometimes, it’s the shipping. We recently did a big book mailing in the same kind of bubble envelopes we’ve always used, and one of our customers sent a photo of how her book arrived:
I can’t even figure out how the post office managed to make that happen, but needless to say, we replaced her book—and are looking into possible UFO involvement.
I agree with all of this, Elizabeth. Like you, I don’t blame the packers, especially the temps and new hires, and it is a stressful job. (I used to pack items far less interesting than books in a warehouse temp job years ago. Ugh.)
But, as you suggest, a little investment up front in better training for the warehouse staff (perhaps even team-wide rewards for lowest number of damages returned, if it’s possible to track that) would prevent a lot of the problems down the line and no doubt end up costing publishers less.
Having also once worked for UPS, I can attest that boxes will be put almost literally through the wringer– huge conveyor belts at every stop where crushing traffic jams and falling boxes are to be expected–so there’s really no such thing as being too careful when packing easily damaged items like books. Of course, if it can be shown that damage occurred while in the hands of the carrier, the publisher can get compensation from them. But so much easier, less costly, and better for everyone’s stress level if the damages can just be avoided in the first place.
And, seriously, why is it *always* the special order with a rush on it that takes the brunt of any damage?
SO interesting. Just received a box of 10 books from a major publisher and one cover was torn and two more had terrible wrinkles in their case covers. Of course I reported it for their records just in case more people are reporting similar issues, and they offered to send more, but didn’t realize this was a ‘thing’. Thanks for the report.
We’ve noticed a dramatic increase in damaged books this fall, especially for events. It’s a real problem.